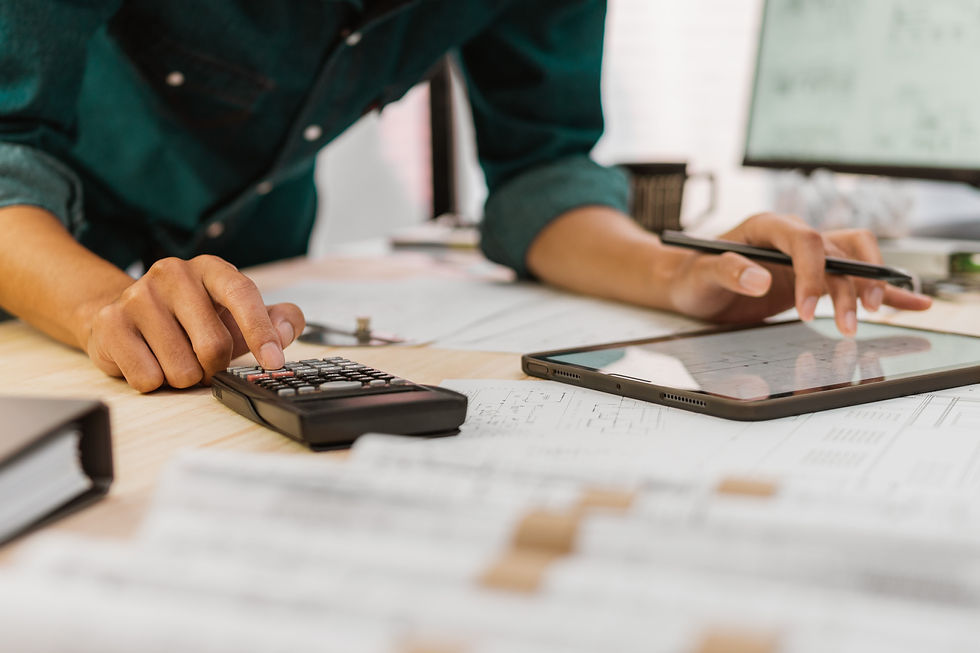
When it comes to executing a successful construction project, one of the key elements that can make or break your budget and timeline is accurate material estimation. Understanding how to perform precise material take-offs and estimations is crucial for staying on track and ensuring the smooth progress of your construction project. In this guide, we'll walk you through the fundamentals of material take-offs and estimation, providing you with valuable insights and tips to streamline your construction process.
What is a Material Take-Off?
A material take-off (MTO) is the process of itemizing and quantifying all the materials needed for a construction project. This comprehensive list includes everything from lumber, concrete, and roofing materials to nails, screws, and other smaller components. Accurate MTOs serve as the foundation for your project's budget, procurement plan, and construction schedule.
The Importance of Accurate Estimation
Cost Control: Precise material estimation helps you create an accurate budget, reducing the risk of unexpected expenses and cost overruns during the construction process.
Resource Planning: With a well-defined list of materials, you can efficiently plan your procurement strategy, ensuring that you have the necessary resources when you need them.
Project Timeline: Accurate estimations also impact your project's timeline. Having materials on-site when they are needed prevents delays and keeps your project on schedule.
Steps to Perform a Material Take-Off:
Project Plans and Blueprints: Begin by thoroughly reviewing your project plans and blueprints. These documents are your roadmap for identifying the materials required for each phase of construction.
Itemization: List all materials needed for each part of the project. Break it down into categories such as structural materials, finishes, plumbing, electrical, and more.
Quantify: Determine the quantities of each material required. This may involve measuring dimensions, counting units, or consulting industry standards.
Consider Waste: Account for material waste and overages, typically calculated as a percentage of the total material required. This ensures you have a buffer for unexpected issues.
Check for Updates: Always stay updated with any design changes or modifications to the project plans, as these can significantly impact your material take-off.
Tools and Software for Material Estimation:
Estimating Software: Consider using specialized estimating software like ProEst, PlanSwift, or Bluebeam Revu to streamline the material take-off process.
Online Resources: Leverage online databases, supplier catalogs, and pricing resources to gather accurate information on materials and their costs.
Consult Experts: Don't hesitate to consult with experienced contractors or industry experts who can provide valuable insights and guidance.
Mastering material take-offs and estimation is a skill that can make your construction project more efficient, cost-effective, and successful. By diligently following the steps outlined in this guide and utilizing the right tools and resources, you can ensure that your project stays on track, on budget, and on schedule.
Remember that accuracy is key, and investing time and effort into your material take-off process will pay off in the long run. Whether you're a seasoned contractor or a DIY enthusiast, these principles will help you achieve construction success.
If you have any questions or need further assistance with your construction project, feel free to reach out to RoMac Building Supply. We're here to support your construction needs every step of the way.
Comments